Video – Why choose timber frame: Faster, smarter & more sustainable construction
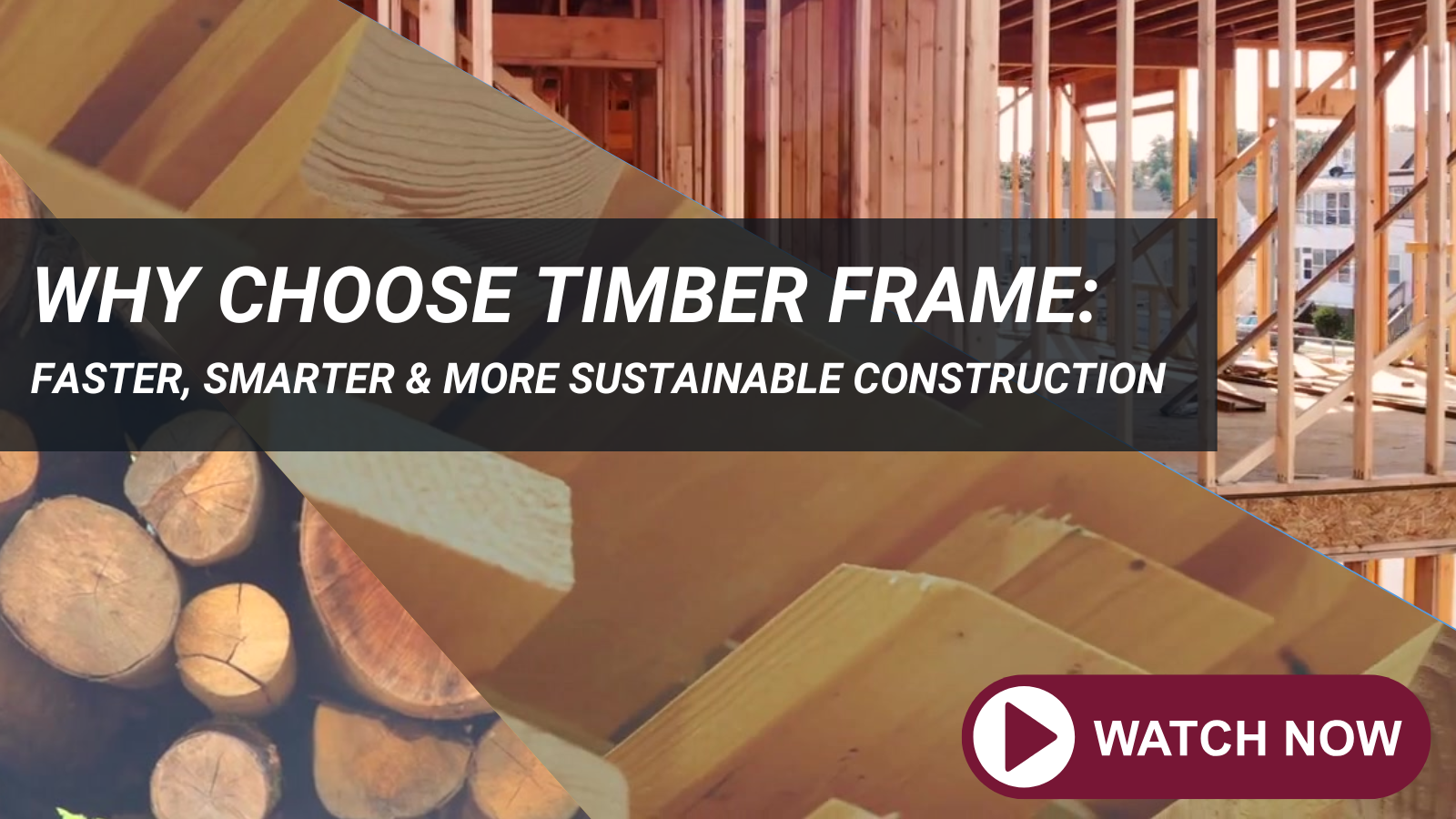
Watch our latest video:
The UK government’s target to build 1.5 million homes over the next 5 years is a huge growth opportunity for developers and contractors.
However, the National Federation of Builders has warned that the projected shortage of 225,000 workers by 2027 could make it impossible to achieve.
“Timber is essential to delivering on the government’s housebuilding mission. With lightweight timber frame systems, we can provide the low-carbon homes we need—right now.”
— David Hopkins, CEO, Timber Development UK
Seizing the opportunity with MMC?
By using Modern Methods of Construction (MMC), it’s possible to build four times as many homes with the same amount of on-site labour. (Source: National Audit Office)
Using modern methods of construction to build homes more quickly and efficiently.
A timber frame solution
Using timber frames offers the most economic structural solution, offering an overall cost saving of 2.8% and a programme saving of 19.5%. (Source: Rider Levett Bucknall, Timber & Masonry Construction Cost Comparison Report)
“[The] STA’s ongoing collaboration with Homes England underscores its commitment to aligning timber construction with national housing strategies, ensuring timber solutions are part of the conversation in addressing housing needs.”
— Andrew Carpenter, CEO, Structural Timber Association
Why does timber frame construction benefit housebuilders?
Faster Construction:
Timber frame buildings can be erected far faster than traditional masonry structures.
Merronbrook’s timber frame approach can decrease the build programme time by as much as 30%.
Reduced Labour:
Off-site manufacture results in faster build times and reduces labour requirements and costs.
Timber frames can save up to three months in construction time. (Source: National House Building Council)
Sustainability:
- The production, processing, and transport of timber frame has the lowest CO₂ cost of any commercially available building material.
- In fact, timber frame has 41% less embodied carbon than masonry. (Source: Committee on Climate Change)
Less Waste:
- Off-site prefabrication reduces on-site wastage and allows for more precise material ordering, lowering costs and environmental impact.
- Timber can be repurposed or recycled, further minimising its carbon footprint.
Quality assurance:
- All Merronbrook’s engineered wood products achieve high-performance ratings for strength, durability, and fire protection.
- Manufactured in a purpose-built facility in Hampshire, UK, with rigorous quality assurance processes to meet stringent safety standards.
- CE Marking and Quality Assurance, through STA, CATG, and ISO standards.
Growth of timber frame
Regulatory changes like the Future Homes Standard and cross industry collaboration with Government producing the Timber in Construction Roadmap is driving timber adoption, reinforcing its role in delivering low-carbon, efficient and high-quality housing.
Timber frame usage is rapidly growing as developers and architects, as well as government bodies like Homes England, recognise that its combined benefits are key to the future of housebuilding.
- Taylor Wimpey, Persimmon, and Barratt Developments have invested in timber frame manufacturing.
- Bellway Homes announced that it is aiming to increase timber frame use to 30% of housing output by 2030.
The value of expert support
Merronbrook’s timber frames, trussed rafters, and floor joists are the perfect choice for developers and housebuilders.
- We offer a complete service, from technical specifications to BIM modelling, as well as on-site training and quality assurance for developments of all sizes across the South East.
- Offering quick and cost-effective construction, while ensuring environmental sustainability.
- We help ensure compliance with regulations like Part L & Z, as well as the incoming Future Homes Standard.
LET’S COLLABORATE TO BUILD A MORE SUSTAINABLE FUTURE – GET IN TOUCH:
📞 01252 844747
📧 webenquiries@merronbrook.co.uk