The benefits of timber frame construction over traditional build
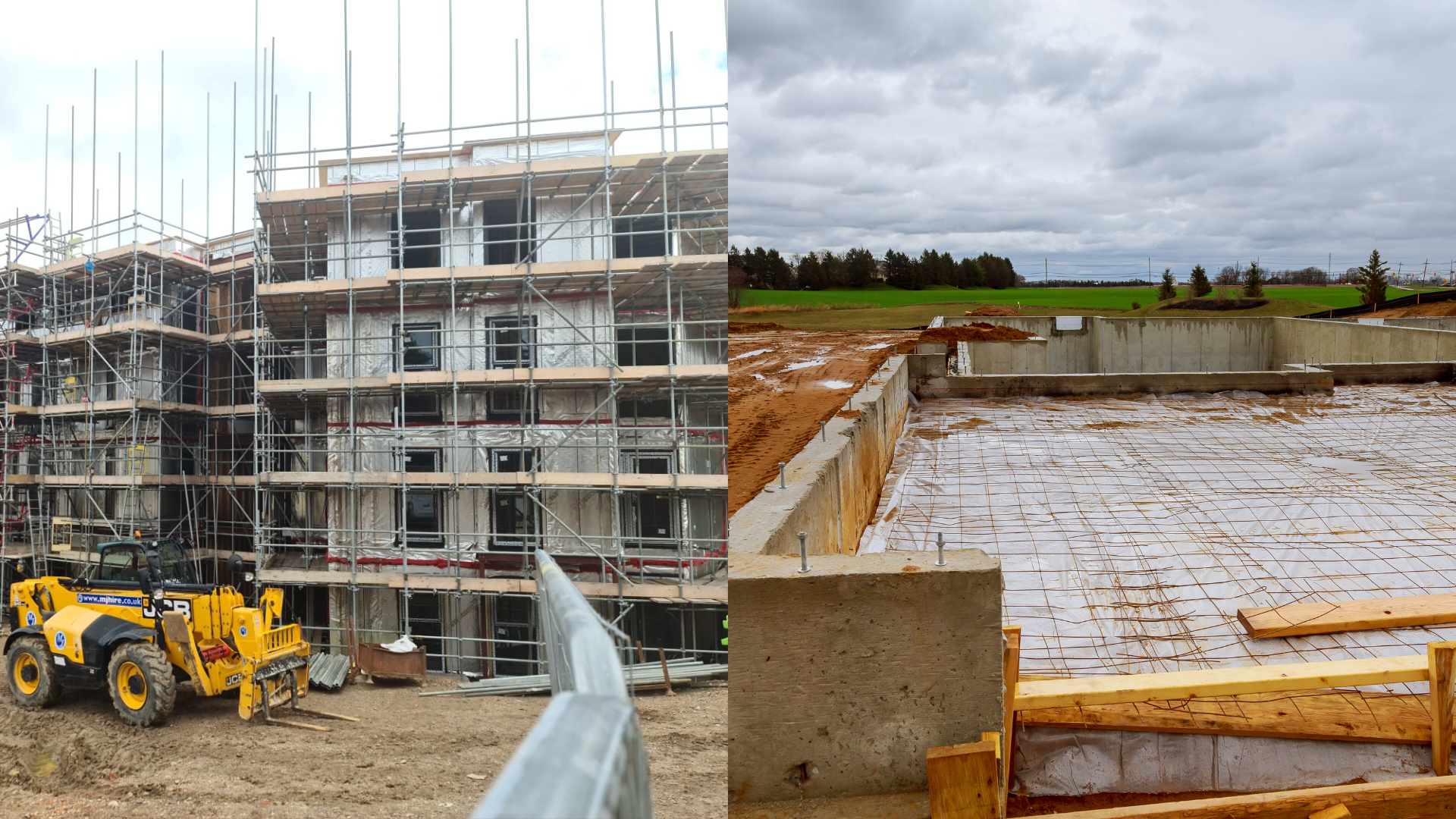
Timber framed construction has grown rapidly in the UK, as developers and contractors alike realise that it is now competitive on costs, but is also significantly faster than traditional alternatives, as well as carrying far more energy efficiency potential.
Traditional versus timber framed construction
There are various methods of construction when approaching a building project, but traditional house building usually means brick and block construction – an approach in which an insulation-filled cavity wall consists of an outer skin made of brick, and an inner one made from concrete blocks. The blockwork inner skin, then bears the load of the structure.
With timber framed construction, the inner blockwork skin would be replaced with a lighter-weight insulated timber panel and structural core. The finished project would look exactly the same from the external facade, but there are fundamental differences.
Timber is a versatile construction material, used in many of today’s construction industry sectors. In 2021 and 2022 timber frame experienced over 30% growth; this sustained growth is set to continue through to 2026 according to reports. Our ever-expanding client base has used timber frame construction in a wide range of projects including private dwellings, low-rise apartments, residential properties, care homes, hospitals, and schools.
https://www.merronbrook.co.uk/sectors/
Manufacturing off-site
Timber frame is an MMC (Modern Method of Construction) product, meaning that 90% of the product will be delivered to the site pre-constructed, depending on the design. This makes timber framing ‘a lot faster than other methods of construction’, concludes self-build planning consultants Self Build Heroes in their assessment. ‘Once the foundations of your self-build home are in place, the timber frame can be erected in a matter of days,’ allowing trades such as electricians and plumbers to get started with wiring and pipework, ready for the second fix elements to progress. The foundations are often engineered significantly lighter when supporting a timber framed dwelling; this is another potential cost-saving element to the build.
Quality, built-In
A significant advantage of MMC over traditional methods is that Quality Assurance processes are built-in at every stage. Merronbrook operates a strict ISO 9001 audited Quality Assurance programme in each of our factories, and then carries Quality out onto the work site, with independent inspections and STA Assure approved Site Safe procedures.
Personalised Design
Merronbrook’s whole service varies from project to project, depending on customer requirements, but we always put YOUR needs at the centre of what we do. We offer our full timber frame kits on a supply and installation basis. Once a project has been secured and designed to the architect’s specifications, our process, and general work cycle is as follows:
• Project-specific measurements are uploaded directly to our semi-automated machinery, and hundreds of unique components are cut with complete precision.
• Digital frame-assembly drawings are delivered to our workstations for assembly. The precision and airtightness offered by off-site construction with factory-fitted insulation is impossible to achieve through traditional brick and block on-site builds. The ‘U’ value performance can’t be matched with brick and block.
• Each finished panel is labelled individually for on-site tracking.
• Once the insulation is pre-fitted, then sheathing ply and breather membranes are applied and secured to panels, using stud marking tape.
• Completed panels are delivered to the site for immediate installation.
This pre-build approach allows construction itself to be much faster. Masonry work, like bricklaying, may have to stop in rain or cold, while timber framing does not. The escalating cost, and lack of availability of traditional building materials, such as bricks, blocks, and concrete, is still an issue. Industry skills and manpower shortages in various building trades such as bricklaying is an ongoing issue too, so the option of quick supply and installation of pre-made components is especially appealing.
https://www.merronbrook.co.uk/benefits-of-timber/
Timber frames and sustainability
Crucial to the recent resurgence in timber framing is the issue of sustainability. There are a number of reasons why timber framing helps meets sustainability targets. The timbers used are PEFC certified so it is an entirely sustainable construction material. Also, timber has much less embodied carbon than traditional building materials (41% less according to this study) and is also a carbon sink, holding carbon in a stable way for generations.
https://www.merronbrook.co.uk/environmental-benefits/
Thermal insulation and energy loss
The UK government recently introduced‘Part L’ building regulation changes bringing stricter rules for the carbon emissions of buildings, with even tighter requirements coming in 2025. (Building Regulations Approved Document Part L 2021, applicable from 15 June 2022.) The ability to accurately calculate and certify whether the insulation within a building will meet the regulations becomes critical.
Under the regulations, a Standard Assessment Procedure (SAP10.2) for new homes in England & Wales currently requires the thermal envelope to be modelled and evaluated for overall quality by a registered On-Construction Domestic Energy Assessor.
This energy loss assessment is much easier to calculate and certify when pre-insulated panels are designed and manufactured off-site. With our pre-determined calculations of thermal losses at party walls, perimeters, and bridging points, building designs can be guaranteed to meet the regulations from the outset.
How expensive is timber frame construction?
Timber prices have fallen back to pre-pandemic levels while other materials continue to rise steadily in cost. But even before that, improvements in methods and materials had made timber framing the most economical option. A 2018 study by construction consultants RLB compared costs to traditional masonry, and found a saving, including prelims, of 2.8%, with a much shorter programme of works.
We are convinced that timber framing is quicker, cheaper and more sustainable, and we would like to prove it to you. Why not contact us on 01252 844747 or webenquiries@merronbrook.co.uk. We’re here to help https://www.merronbrook.co.uk/consultancy/